Moving a warehouse and changing the sales process can be a daunting and overwhelming process. As your business grows and you streamline your supply chain, you may need to increase or decrease the number of warehouses that you occupy in order to move your inventory. You should pay a lot of attention to organizing the inventory the day before moving your warehouse.
This is the first thing you should consider on your Warehouse Relocation Checklist. When it comes to any type of removal, the most important thing is to find a reliable warehouse relocation service. The worst possible scenario for a well-organized relocation is the realization that you do not have enough space for your entire inventory. Now that you have a basic checklist to help you implement a successful relocation, it’s time to take action. This step-by-step guide will help save time and save headaches during a major move and ensure that your stock move goes as smoothly as possible.
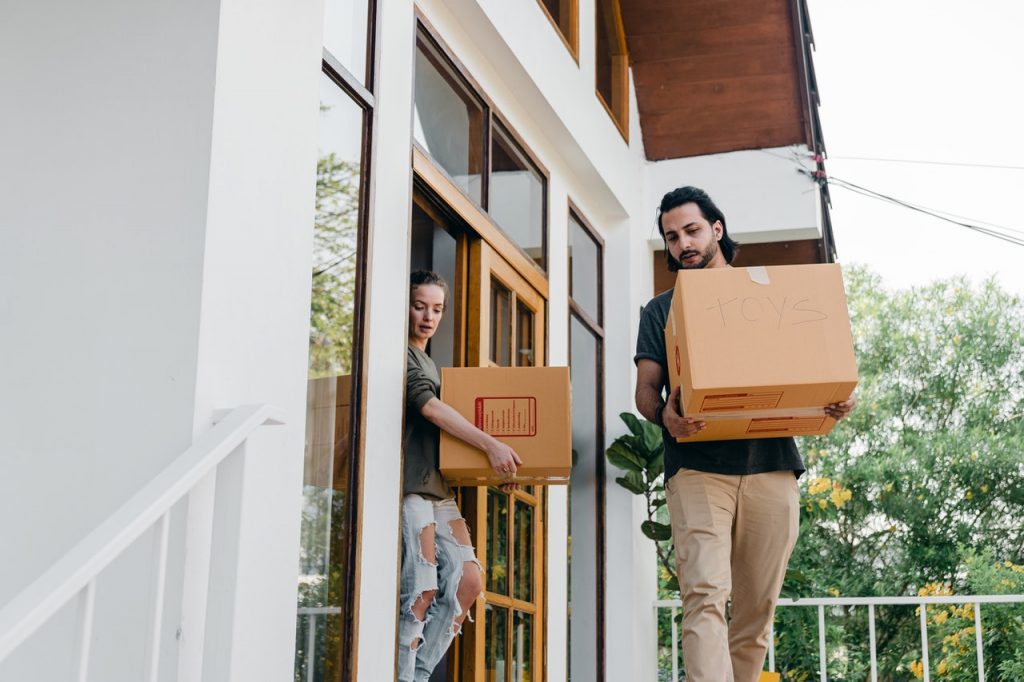
Analyze the advantages and disadvantages of your current stock layout, draw up a plan based on your insights and pay attention to the details. Before moving, make sure you know what permits are required and what restrictions apply to your new premises. If local building inspectors or fire inspectors want to be involved in the new warehouse planning, they should be on board. Escape lanes, sprinklers, and car parks are all under the influence of the authorities, the sooner you contact them the better.
Communication with employees should be at the heart of your relocation plan. If you are trying to organize the relocation of the warehouse, appoint several employees to help you organize your inventory.
As you can see, there are several rules for planning and organizing a relocation. You can simplify the relocation process by following a checklist, but before you go any further, you should get the relocation checklist that will guide you through your relocation. This checklist helps you to process the move more efficiently. Once you have a plan for your new warehouse layout, go through it and make sure it is as detailed as possible. Once it is detailed, it will have a few questions to ask before moving. This is our first item on our Warehouse Relocation Checklist to tick off the things you need to work on. This checklist of essential tasks helps you plan your move to a new warehouse and make the process run smoothly. The more work and organization and planning your warehouse does, the stronger it will be.
Check current logistics processes and identify strengths and opportunities. Design warehouse layouts with the flexibility to adapt to changes and growth in the business, including opportunities to expand. Run new IT systems in parallel to existing systems until the new warehouse is fully functional. If you have outgrown your current warehouse, you may need to move to a larger store. The location of your new warehouse is the key to reducing transport costs and increasing the response time to demand. To get the layout and design of your warehouse, follow the steps for moving your warehouse.
When you move to a new warehouse, you need to plan and design your pallet and shelf system. Existing designs for your current warehouse may not make sense for your new location. Choosing the best location for your new warehouse is an important part of your relocation plan. If you want to relocate your warehouse, it makes sense to move to a location that offers more benefits than your current warehouse. The two most important things to bear in mind are the size and location of the new site.
You can continue operations in your existing warehouse or start operations in your new warehouse. If you continue operations after moving, it is advisable to overlap the use of your two warehouses. This can be difficult to handle, so it is important to separate the different operations so that you can operate each warehouse independently.
Shifting your warehouse means that your warehouse will be out of service for a period of time. In this case, you intend to demolish and reinstall your current warehouse. If your business has a consistent commercial relocation service partner, consider their stock relocation options. If these options are not available, look for a commercial relocation service partner that offers relocation services. Ask potential commercial relocation service partners if they can offer a complete solution for your warehouse transports.
It is a wise decision to choose a company that specialises in moving warehouses. Warehouse removals companies have expertise in key areas such as transporting heavy machinery, and they often have specialized equipment, such as high-performance forklifts, that normal 3PLs do not have. Specialists in this area will probably be able to offer a consistent logistics solution.
Assess your current warehouse planning process and get an idea of how your new space will move to something more complex and challenging. Not only is it difficult to move heavy storage racks, pallets, and inventory, but there are also many additional logistical problems. If you want to relocate your warehouse, it makes sense for you to move to a location that offers more benefits than your current warehouse. Choosing the best location for your new warehouse is a key part of your relocation plan.